Lifestyle
A Comprehensive Guide to Cold Solder Joint
Soldering is one of the most important procedures in putting together an electronic circuit; yet, it is also one of the phases that might be the starting point for an electronic circuit’s unreliability. Creating a cold solder connection is the most prevalent problem that might arise during soldering.
What exactly is a junction made using cold solder?
After reading the explanations given above, it should not be too difficult to understand what a cold solder junction is. A coldsolder joint is produced when the solder wire is not heated properly during the soldering process, resulting in an imperfect union.
It is also possible for there to be a cold solder connection if the board or the soldered wire is disturbed before the liquid solder solidifies into its solid state.
A cold solder junction will increase electrical resistance at that joint if it is not recognised or corrected promptly. The worst-case situation is the possibility that the joint will not conduct electricity at all, which would lead to the breakdown of the board.
A variety of cold solder joints are available
There are a few different cold solder junctions, and each type has unique behaviour and a set of reasons. The most frequent kinds of cold solder junctions are discussed here.
Cracked solder joint
As the name indicates, a cracked solder joint is the outcome of a strained solder junction that gives way to producing a crack. After the fracture has formed, the pin will be partly separated from the board and free to travel about. Depending on the shape of the fracture, this movement may either close or break the electrical connection.
The start and stop of the uncontrolled electrical connection will cause the device in issue to function well or not properly on occasions that seem to be completely at random.
As a direct consequence of gravity, the components that are installed vertically and are very heavy are the ones that pose the most risk. The issue will become much more severe as the fracture continues to spread if the boards are constantly being flipped or moved.
Dry solder joint
A junction solder joint with an inadequate quantity of solder is referred to as a dry solder joint. The whole connection becomes moist when the liquid solder pours into the joint. This allows for a flawless electrical connection to be created after the solder has cooled and solidified.
A dry solder does not contain a sufficient quantity of metal, which might result in an entirely open circuit in certain circumstances. In other situations, the joint may have sporadic electrical conductivity and high resistance, which results in noise whenever it is put into use.
Cold solder joint
A junction that has been cold soldered is often either broken or dry, depending on the circumstances. The fact that it is ineffective serves as the defining trait. In most cases, a cold solder joint is to blame when you are unsure if the junction in question is cracked or dry, but it does not seem functioning properly.
Sometimes the junction formed by cold soldering might be dry and broken simultaneously. Despite this, not all cold joints are comprised of fractured solder joints. Even yet, this does not change the undeniable truth that a damaged solder connection will, at some time in the future, cause problems if it is not repaired.
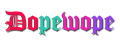