Technology
Broaching – A Basic Overview
Broaching is the process of machining metal parts using a toothed tool called a broach. There are two major types of broaching: linear and rotary. In either case, the toothed tool will remove material and shape the metal. Here is a basic overview of the process. If you want to learn more, keep reading. This article will cover both. Whether you choose linear broaching or rotary broaching, you can be sure you’ll get the best results.
The process of broaching produces internal keyways or splines in a pulley or gear. This shape is the most common, and broaches are often used to create these shapes on gears, sprockets, or hubs. They can also be used to enlarge round holes or cut other external shapes. The type of broach you use depends on the part you’re working with. In most cases, internal broaching will produce round holes.
The advantages of broaching over other machining processes include high accuracy and surface roughness. While the latter is better for creating complex machined surfaces, broaching is best for soft metal. Hard metal, on the other hand, will cause the tool to quickly become dull and useless. Typical applications include machining internal round holes from six to one hundred millimeters in diameter, as well as external flat surfaces with a large range of contours. Among these applications, broaching is the only process that can machine spline holes, which are difficult to achieve through other methods. Here are some of the different types of broaching operations. Shop broached items from Somma Tool.
Surface broaching is a straightforward process, involving moving a workpiece against a stationary surface broach. Then the tool moves up in the opposite direction. A spline-profile broach has the highest profile of the two types, but other types have similar geometries. When choosing a broaching machine, keep in mind that the best machine for your particular job will depend on its size. A servo table-up broaching machine will finish your job in minutes.
The benefits of a broaching process are significant. First, this process is used to machine high volumes of parts with repetitive, complex cuts. It works best on materials with a hardness rating of 26-28 Rockwell C. But production companies have also used materials with a higher hardness rating. A new broach can make up to 8,000 cuts, but properly cared-for ones can have as many as 60,000. So, if you’re looking for a machine to make your next-generation car, broaching might be a great option for you.
Another benefit of broaching is that it produces a high-quality finish. Its fast cutting speed makes it suitable for mass production. Broaching also leaves the finished product with good dimensional stability. The tools and machines used for broaching are made specifically for this type of production, making quality data more stable. Moreover, the tool itself is designed for mass production. A simple index-able insert broach, for example, can help you achieve higher precision and longer tool life.
A common method of finishing metals is broaching. This machining method involves using a tool with several sharp cutting edges called broaches to remove material from metal parts. The tool can also be used for irregularly-shaped metal parts. The broach is a great choice for machining small-to-medium-sized parts. You can also use it to machine screws. There are many advantages to broaching. Its main downside is that it is not practical for larger work-pieces or removing large amounts of stock.
While prevention is impossible, there are some simple preventative measures you can implement. These will depend on your boat’s type and size. However, the basic precautions that are necessary to prevent broaching include keeping the backstay on downwind. A backstay, when used properly, can be a great preventive measure for a boat that is too heavy to handle the wind. If you don’t have a backstay, you risk depowering the mainsail.
The two most common types of vertical broaching machines are the push-up and pull-down models. Push-up models are generally more economical, but vertical machines are best for large workpieces. They can also be classified according to the direction of tool feed. Both types of machines can perform different operations and are versatile in many different ways. However, vertical broaching machines are ideal for internal and surface broaching. In either case, the tools are held in special heads.
The primary difference between interior and exterior broaching is the type of tool that is used. A surface broaching machine uses a cutter that can pass over the surface of a workpiece. The cutting tool is attached to a ram and can move horizontally or vertically. A machine with two rams is known as duplex broaching. The latter type of broaching requires a starting hole and two rams. This method of finishing can be done quickly and easily.
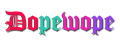