Business
Why Choose CLT Detailing
To add the finishing touch to CLT detailing, you should detail exposed faces and edges. In addition, you should detail panel joints and rough openings. Detail 14a and detail 14b show some recommended detailing for panel joints. After completing the detailing, you should inspect the panels for spline alignment. A cleated joint is an effective and efficient way to attach CLT panel edges. After installing CLT panels, you can finish them with stain, paint, or stain-grade sealant.
Cross-Laminated Timber (CLT) is a mass timber product composed of multiple layers of structural and dimension lumber. This engineered wood panel material is often used for walls, floors, and roofs. The DowcoCompany offers Mass Timber models that incorporate CLT detailing. Dowco knows the importance of accurate CLT BIM modeling. A well-executed CLT detailing process will save time and money, and ensure a durable, cost-effective structure.
CLT panels can be used to build walls, floors, ceilings, and roofs. They are assembled in a factory and delivered to the site. Because CLT is structurally sound, it doesn’t require cladding. It’s also versatile and can be used for other projects. Adding CLT detailing to an existing project is an excellent way to add character and style to your project. But how do you choose the right style?
The CLT Handbook provides detailed information on how to detail CLT connections. Many engineers without extensive experience in building mass timber structures use exposed steel hardware. While this is less visually appealing, it also performs poorly in a fire. If your project requires a high fire-resistance rating, you should choose a CLT connection that allows the screw heads to be exposed. A CLT connection that features only screw heads is an effective design solution.
Pre-applied coatings can limit CLT moisture uptake. Pre-applied coatings are especially valuable at panel edges because moisture uptake is faster through wood end-grain. However, pre-applied coatings may not be effective as a sole means of protection in high-risk regions. Further, they are not 100 percent effective in prolonged exposure to moisture. A poorly-applied coating can cause dimensional changes, microbial growth, and general deterioration of the enclosure’s components.
Another advantage of CLT is its versatility. It can be used as a substitute for concrete. CLT is environmentally friendly and could be cost-competitive for buildings with more than six stories. Further, it can be fabricated off-site. This makes it easier to assemble CLT structures in a shorter time, regardless of the season. Also, CLT structures can be installed faster and easier than concrete ones. These advantages allow CLT to be a competitive material for multistorey wood buildings.
Roof insulation and panel/structure insulation are critical to the overall look of CLT structures. It prevents vapor diffusion into the roof assembly. The roof underlayment also provides temporary moisture protection. Get Rebar Detailing now. If the CLT panels are not installed properly, ponded water may pass through the membrane. However, over the course of 24 hours, this water will not be able to penetrate the membrane. This is why it is essential to properly detail CLT roof assemblies.
Fire resistance is another benefit of CLT. The char on the panels forms a protective layer that slows the spread of flames. When properly maintained and installed, CLT elements will not rot or acquire mold. The main concern, of course, is preventing moisture from getting into the wood. Proper detailing and the use of coatings, sealants, and flashing will protect the CLT elements from direct contact with moisture. And it will prevent mold growth as well.
A proper moisture management plan should outline all steps to limit moisture exposure to the CLT elements. Building codes generally require that the wood’s moisture content be 16-19 percent before covering it. Get in touch with Dowco to get Bridge Detailing.While this is a reasonable standard, it doesn’t address the hygric mass that is characteristic of mass timber elements. Hence, it is important to maintain a moisture content of 16 percent or less at all locations. For better performance of CLT assemblies, a thorough moisture management plan should be prepared before construction begins.
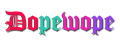